Sustainable Manufacturing Practices in Modern Foundry Operations
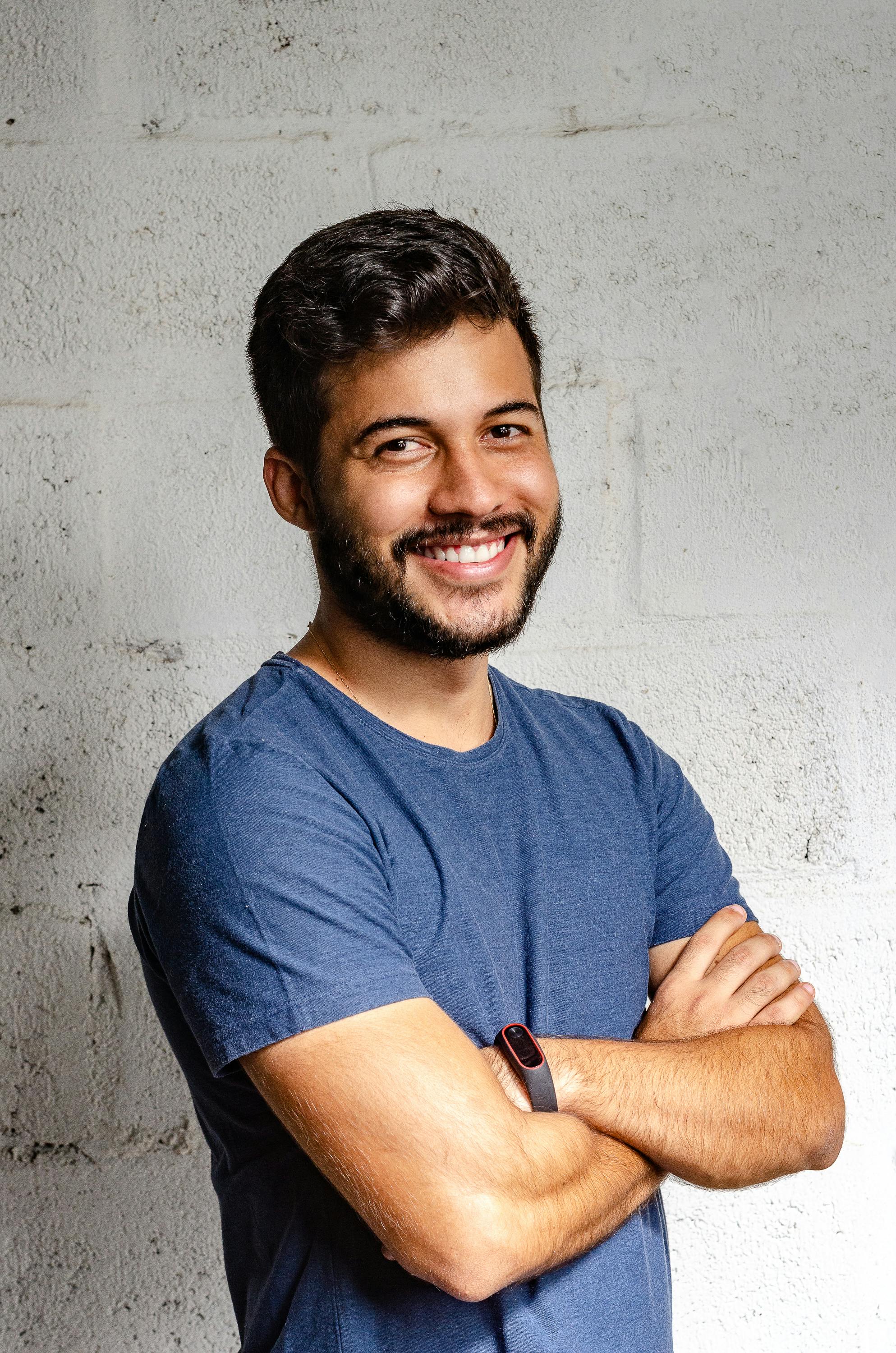
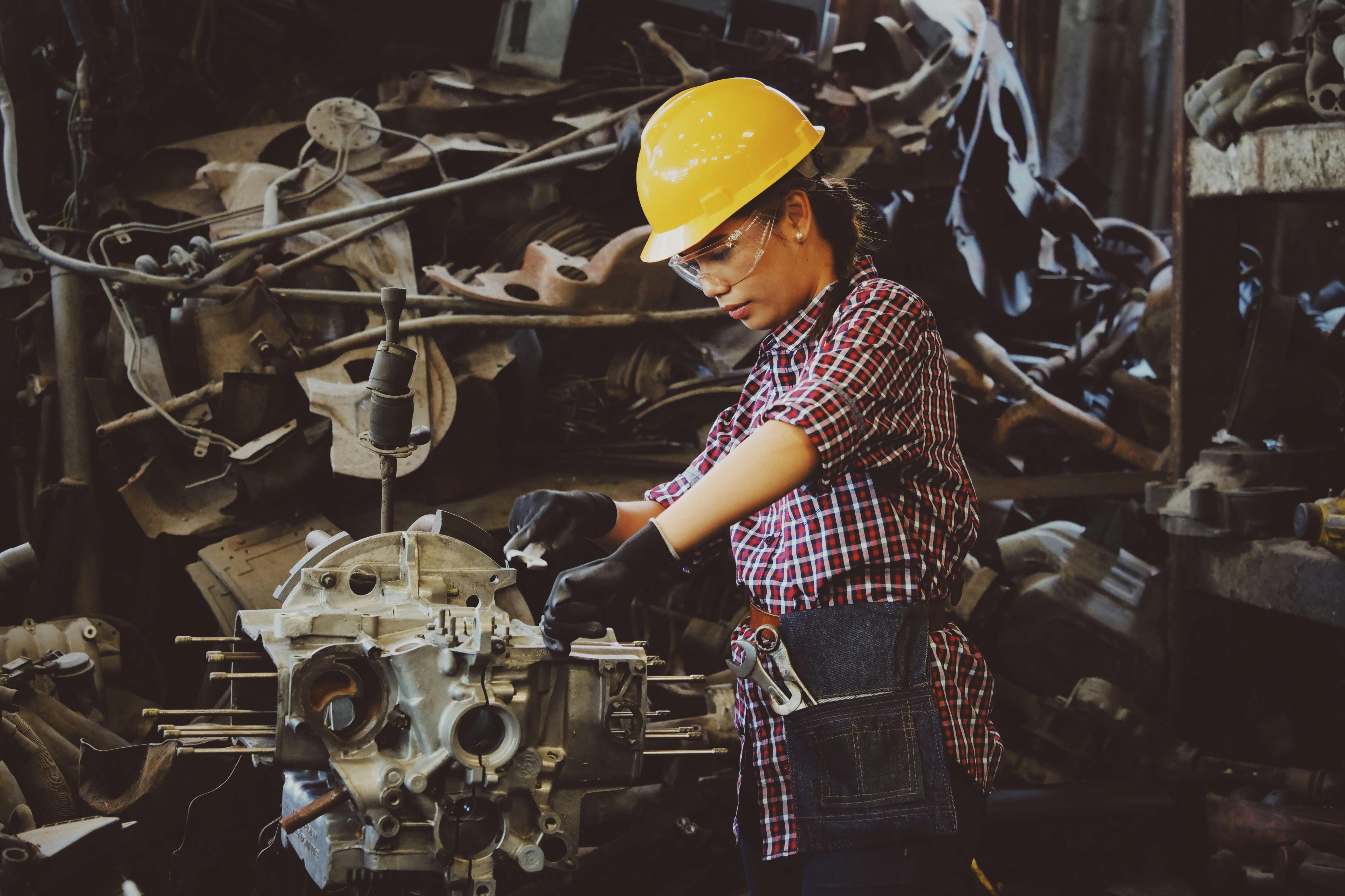
Embracing Sustainability in Metal Manufacturing
The manufacturing industry, particularly metal foundries, has traditionally been associated with high energy consumption and environmental impact. However, at White Rock Foundry, we're leading the charge in implementing sustainable practices that reduce our ecological footprint while maintaining the highest standards of quality and efficiency.
1. Energy Efficiency Innovations
Energy consumption represents one of the largest environmental impacts in foundry operations. Modern foundries are implementing a range of technologies to reduce energy usage, from high-efficiency induction furnaces to waste heat recovery systems. At our facilities, we've installed advanced energy management systems that optimize power consumption in real-time, resulting in a 30% reduction in energy use over the past five years.
2. Closed-Loop Water Systems
Water conservation is another critical aspect of sustainable foundry operations. Our state-of-the-art closed-loop water systems recycle and reuse water throughout the manufacturing process, dramatically reducing freshwater consumption. Advanced filtration and treatment technologies ensure that any water eventually discharged meets or exceeds environmental regulations.
3. Metal Recycling and Waste Reduction
Metal casting is inherently conducive to recycling, as scrap and runners can be remelted and reused. We've taken this principle further by implementing comprehensive waste reduction programs that minimize material waste at every stage of production. Our advanced simulation software helps optimize gating and riser systems, reducing excess metal while ensuring perfect fills.
4. Sustainable Sand Reclamation
For sand casting operations, sand reclamation represents a significant opportunity for sustainability improvements. Our thermal and mechanical reclamation systems allow us to reuse up to 95% of our sand, dramatically reducing waste sent to landfills. The small amount of waste sand that cannot be reclaimed is repurposed for construction applications rather than disposed of.
5. Low-Emission Binders and Coatings
Traditional foundry binders and coatings often contain volatile organic compounds (VOCs) that contribute to air pollution. We've transitioned to water-based and inorganic binder systems that significantly reduce emissions while maintaining or improving casting quality. These advanced materials not only benefit the environment but also create healthier working conditions for our employees.
6. Life Cycle Assessment and Continuous Improvement
Sustainability is not a destination but a journey of continuous improvement. We regularly conduct comprehensive life cycle assessments of our products and processes to identify opportunities for environmental improvements. This data-driven approach ensures that our sustainability efforts are focused where they can have the greatest impact.
The Business Case for Sustainability
It's important to note that these sustainability initiatives aren't just good for the planet—they're good for business. Energy efficiency reduces operating costs, waste reduction improves material utilization, and sustainable practices help attract and retain both customers and employees who value environmental responsibility. Our experience has shown that sustainability and profitability go hand in hand.
Conclusion
The future of foundry operations lies in sustainable manufacturing practices that reduce environmental impact while improving efficiency and quality. By embracing these innovations, White Rock Foundry is demonstrating that traditional manufacturing can be transformed into a model of environmental responsibility without compromising on performance or profitability. As we continue to innovate and improve, we invite our industry colleagues to join us in building a more sustainable future for metal manufacturing.
Engineering Excellence & Innovation
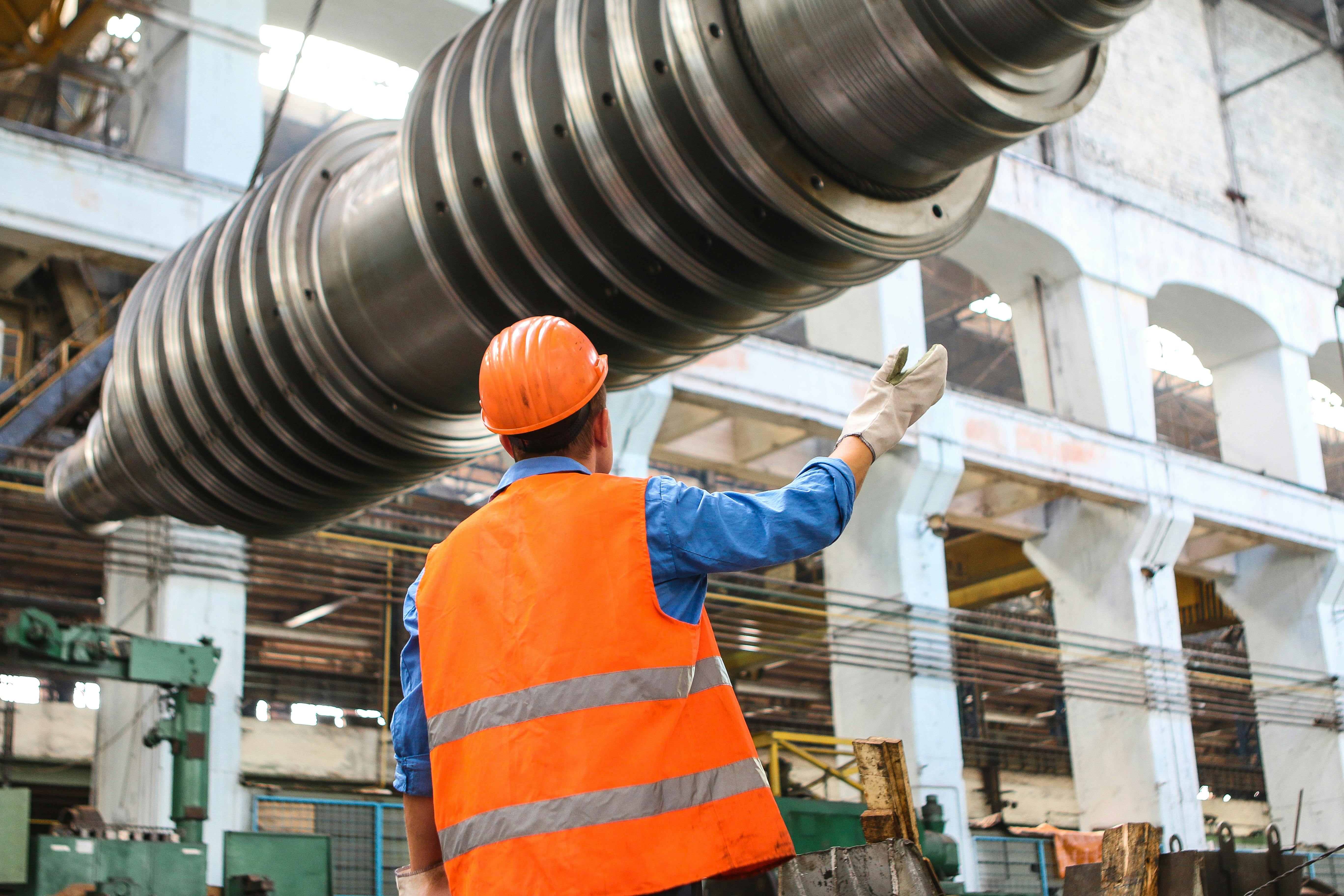
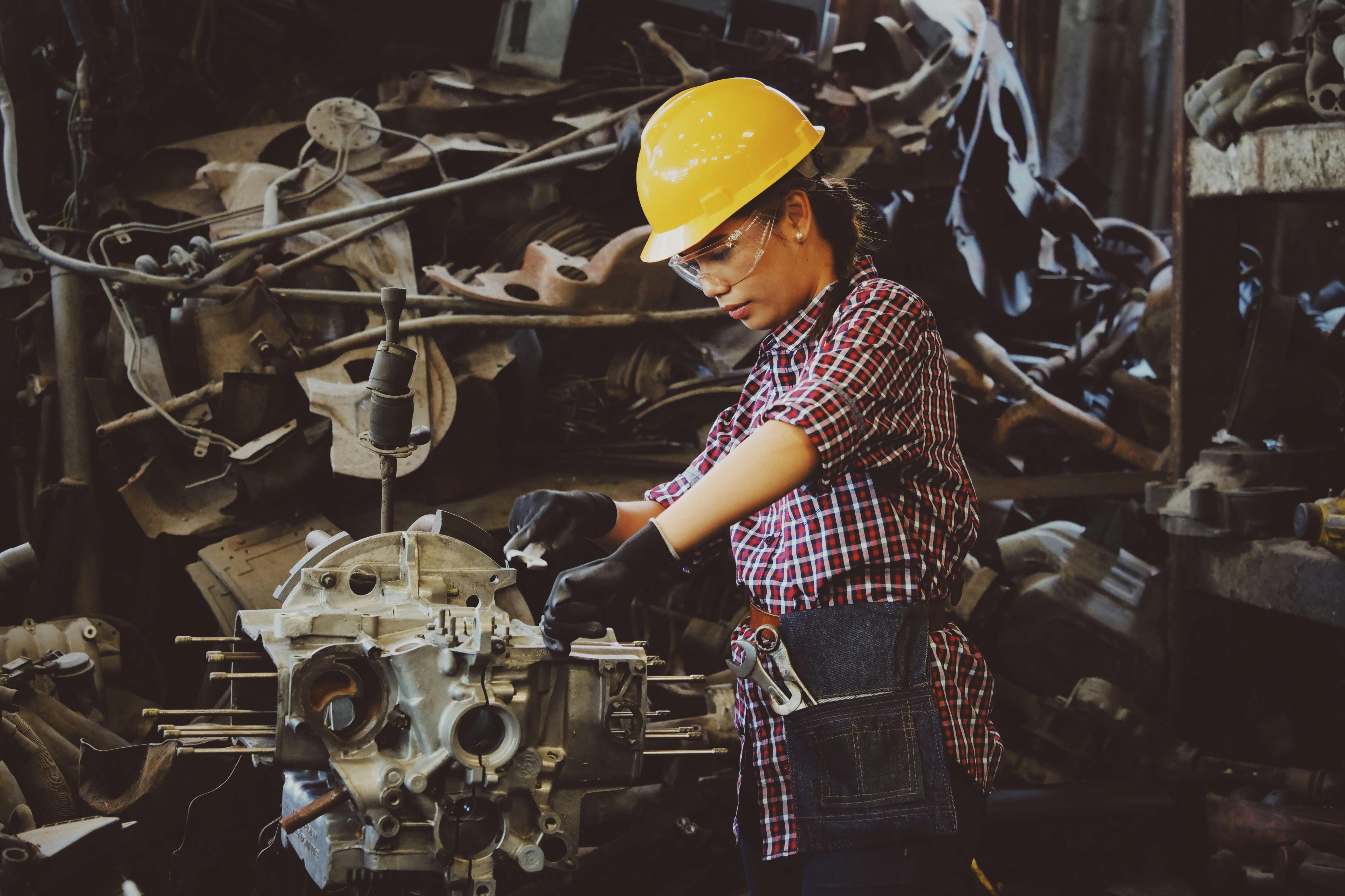
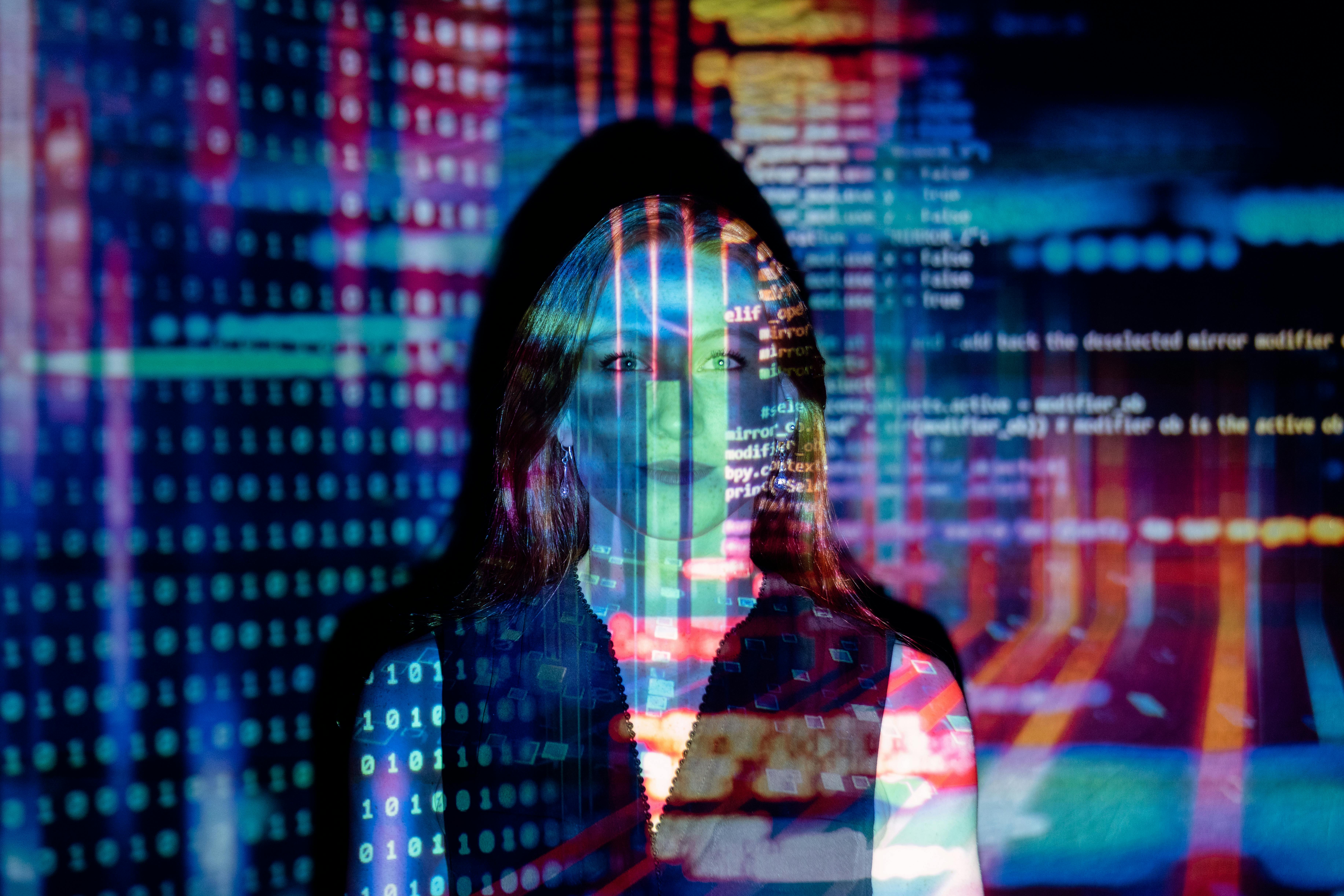
Recent Posts
May 6, 2023
Precision Metal Casting InnovationsJune 12, 2023
Sustainable Manufacturing PracticesJuly 23, 2023
Digital Transformation in Engineering
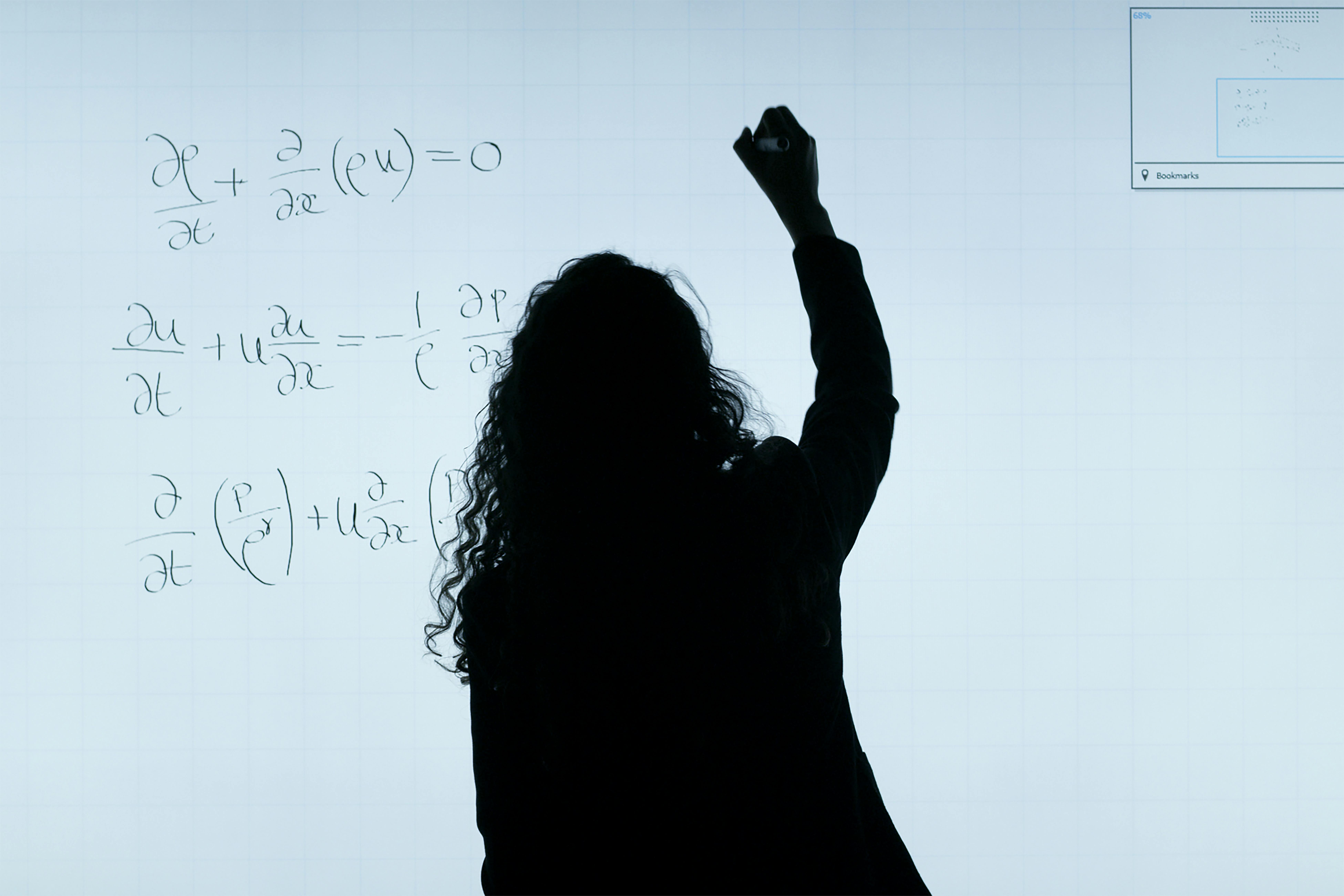
From concept to creation,
we've got you covered.
Contact us today to experience precision engineering solutions tailored to your manufacturing needs!